As said before, i stumbled over an issue..
I let the game on to test it, and after a while it sounded like a rocket taking off..

Oviously it was the fan in the pc making overhours as there was not enough fresh air circulation in the closed cabinet.
The coinslot in the top alone is not sufficient

Let's take care of that !
I took a piece of scrap wood to figure out where i could position an air out take which i constructed out of some 40mm plumming PVC.
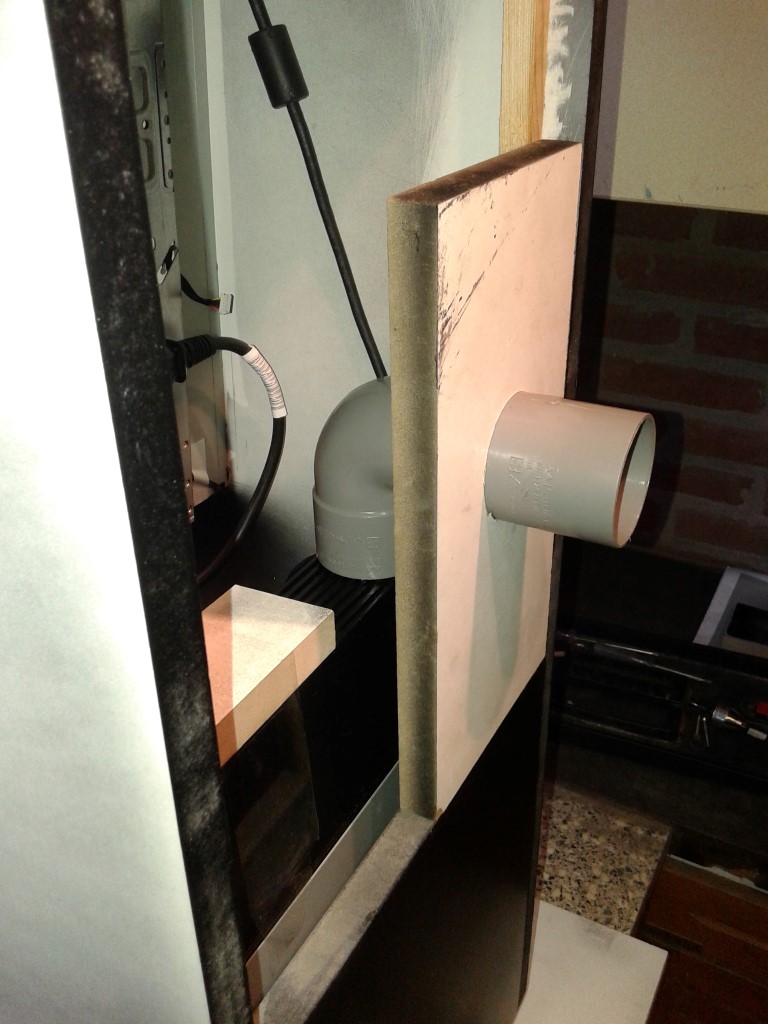
the reason i took 40 is that it will connect nicely with the size of the back of the pc.
There is a plastic cover on the back of the pc to hide the cables.
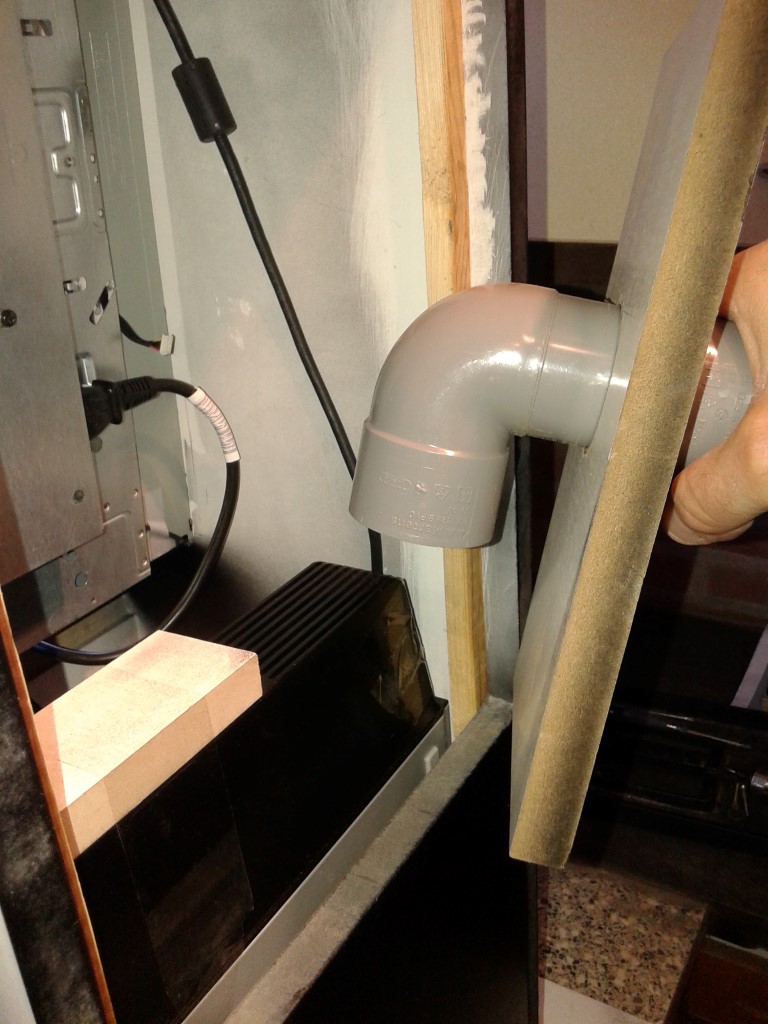
And the second reason is that i have a "sawdrill" of that size.

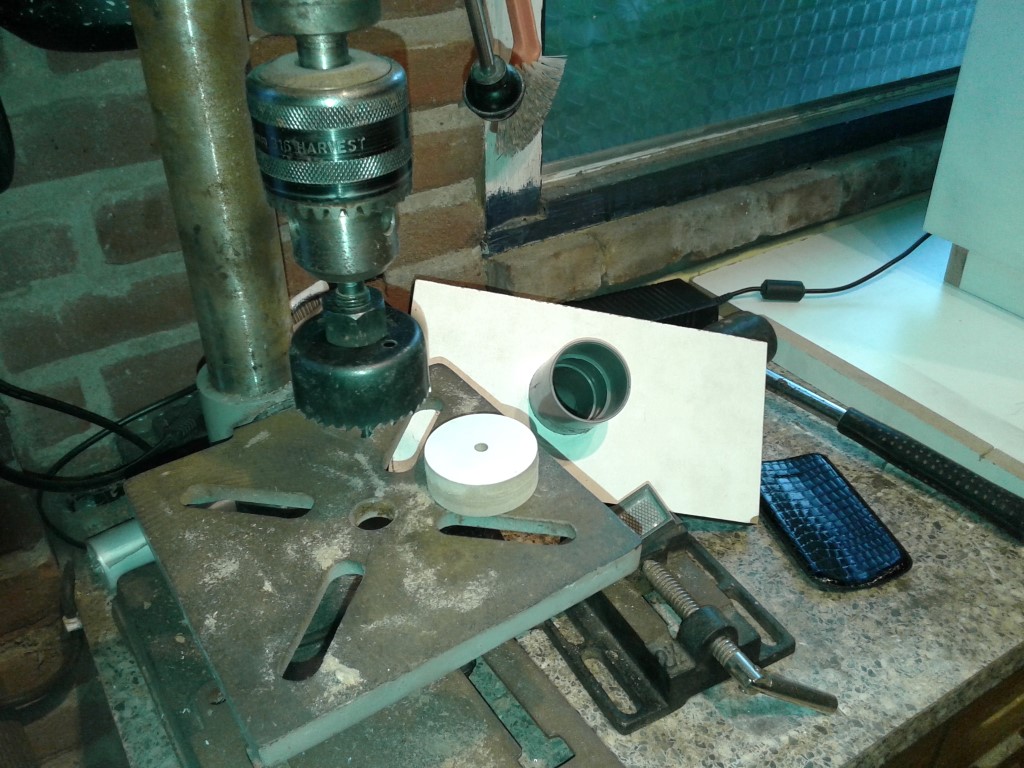
I used that piece of scrap to transfer the position of the hole onto the backdoor.
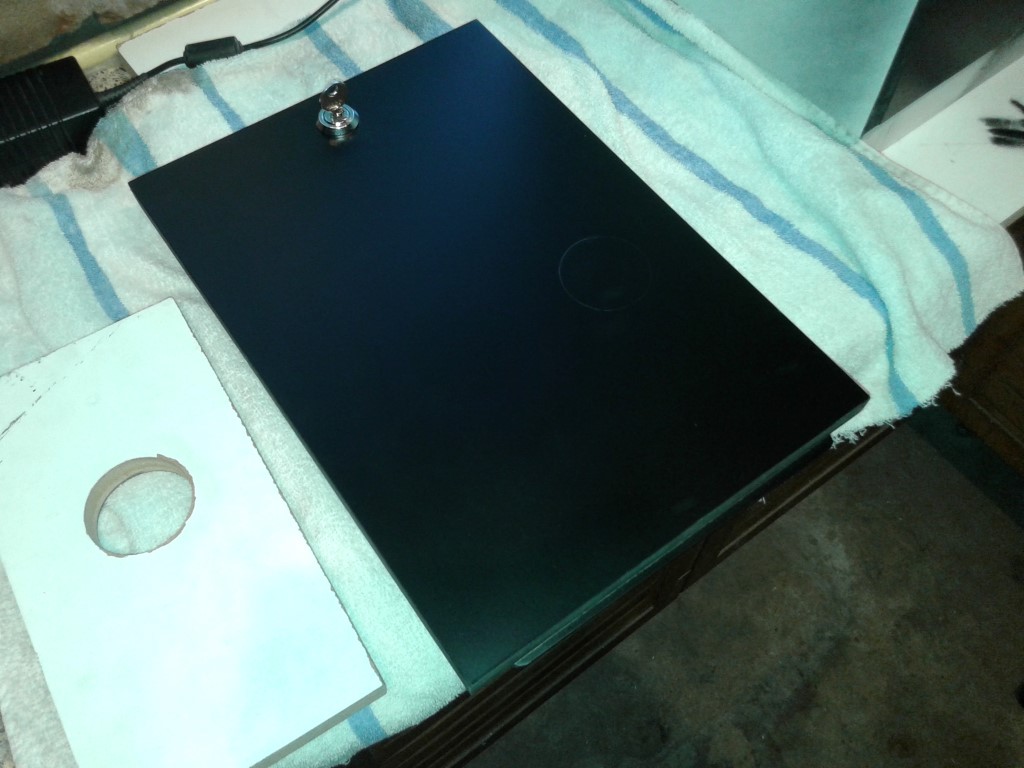
Let's drill that hole !
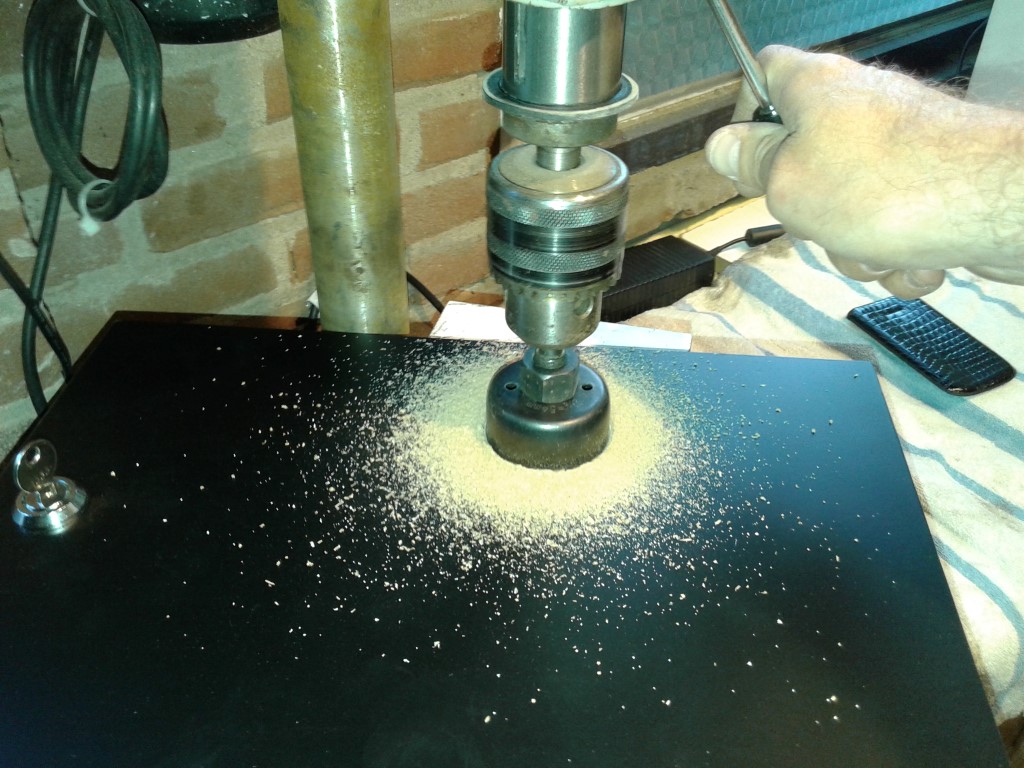
I drilled it from both sides to prevent damage to the already painted backdoor..
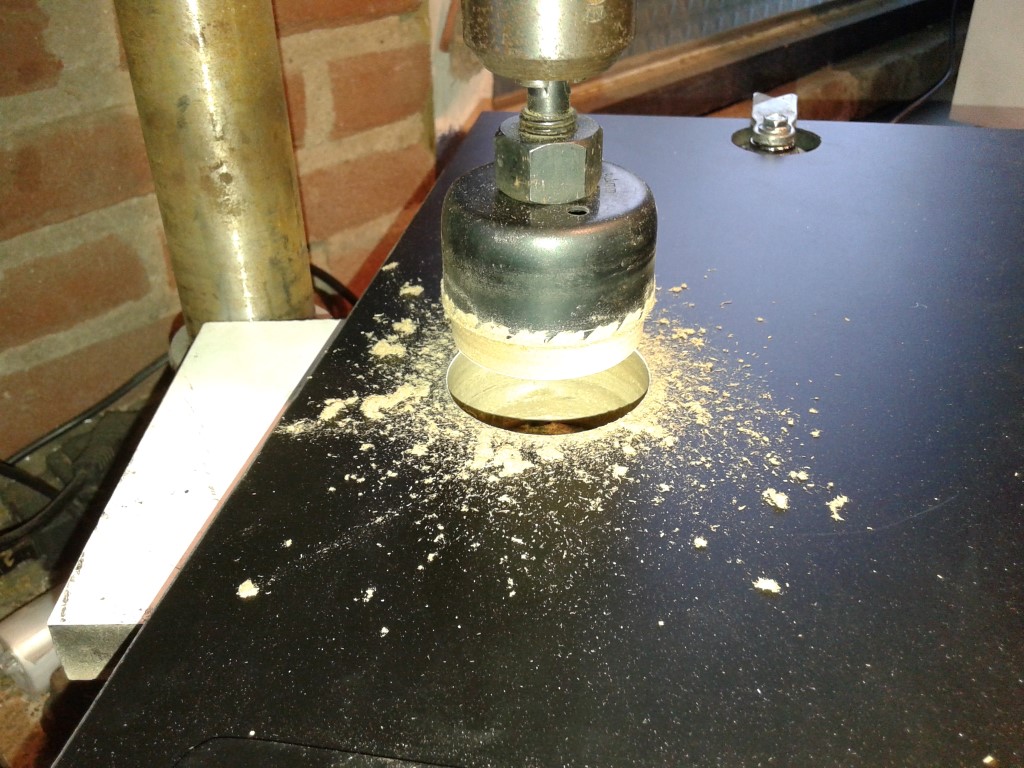
Hole in place, but there is some damage to the paint afterall..

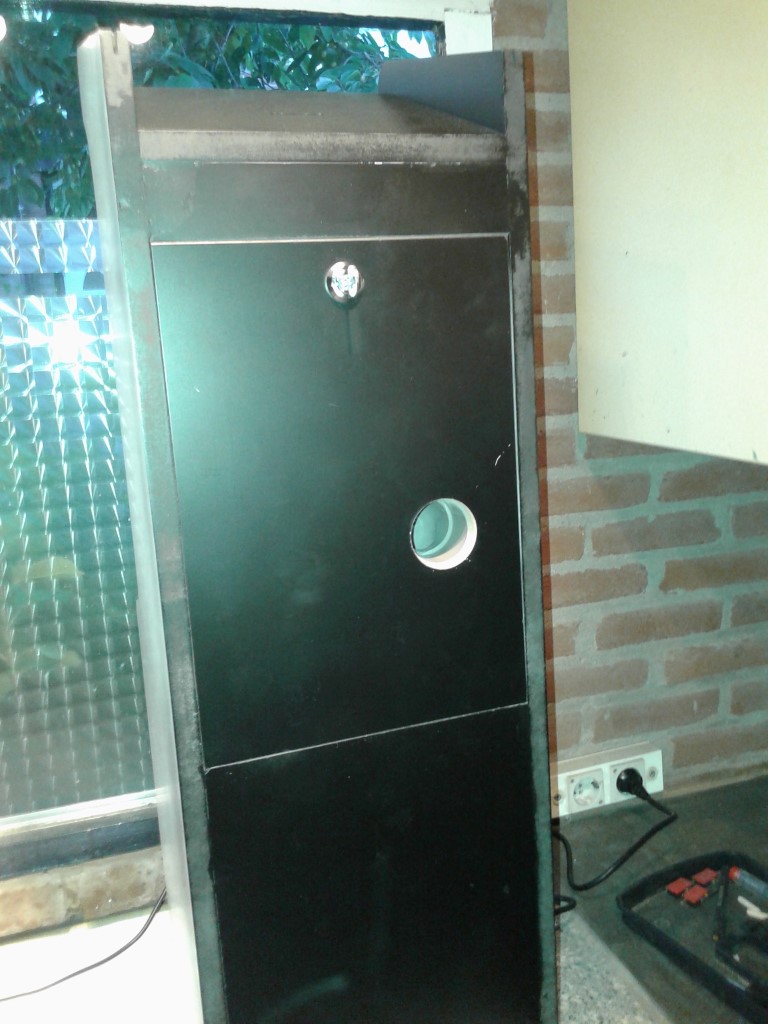
Testrun time !
Much better than before, not too much noise anymore. :spaceace:
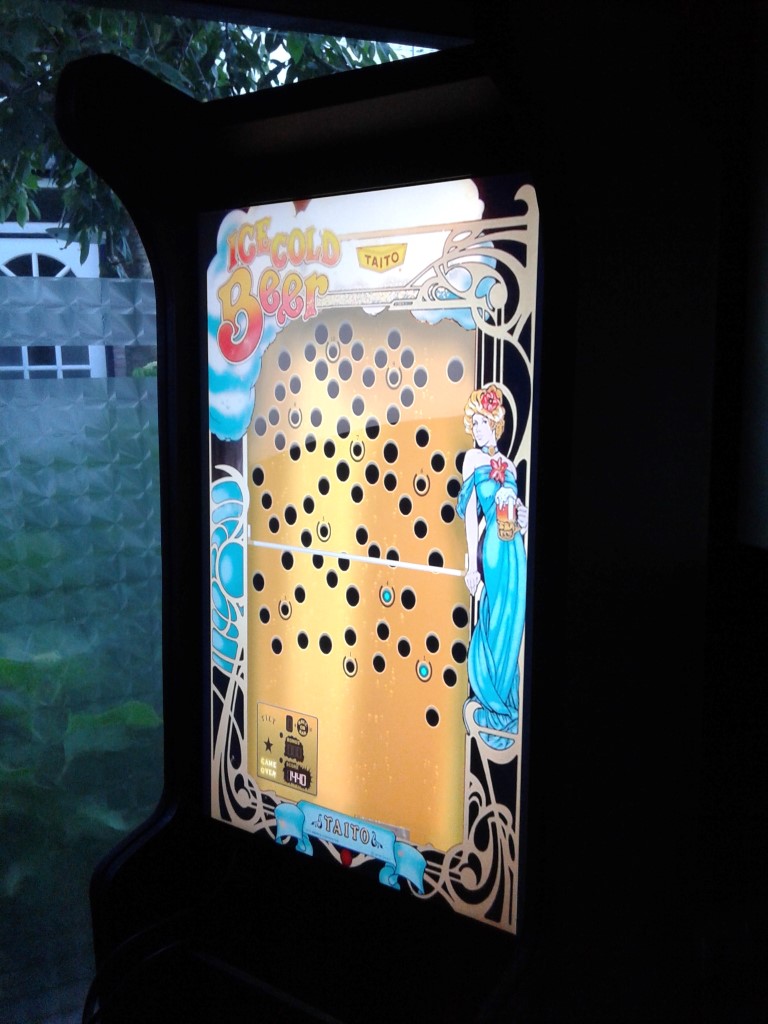
Again a profit when you have some old pc equipment on hand, nice fangrills to salvage !
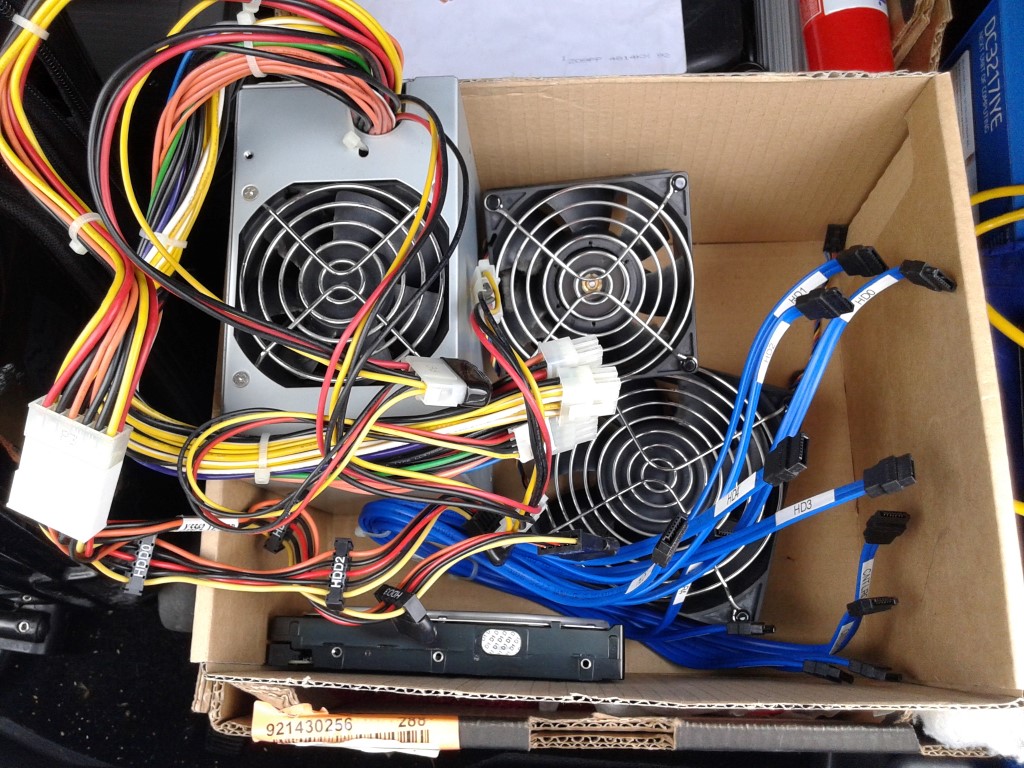
I failed bigtime with touching up, i had paintrunners which i tried to wipe off...
Not a good idea.... :roll:
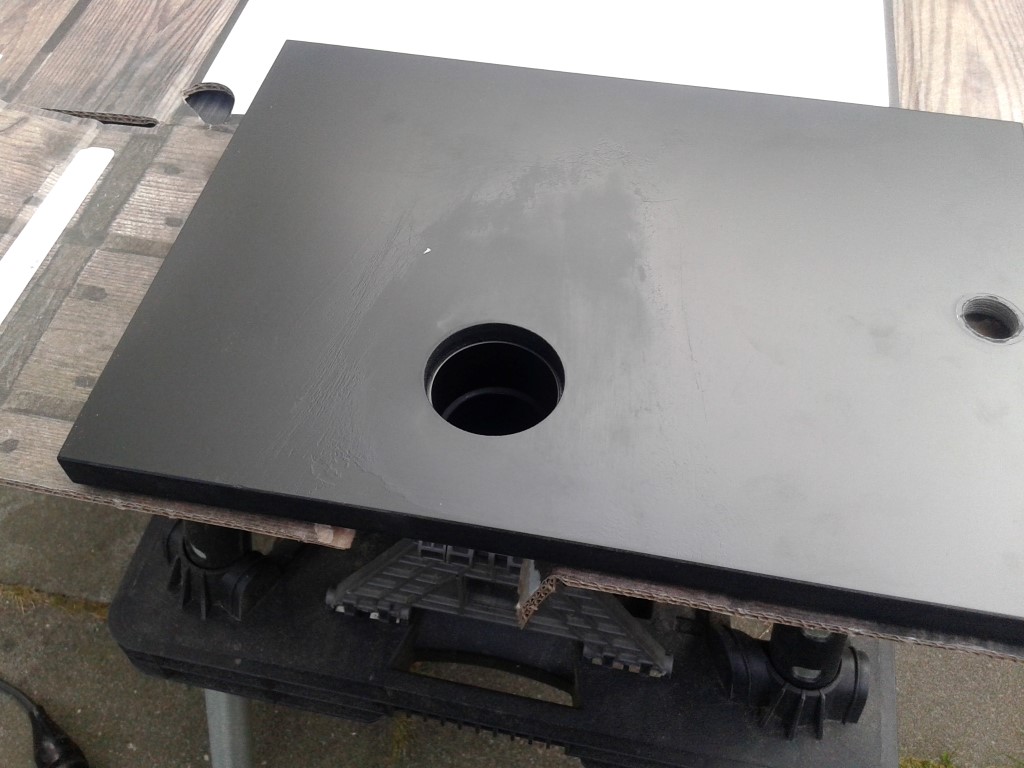
The only way to fix that is to redo all the paint..
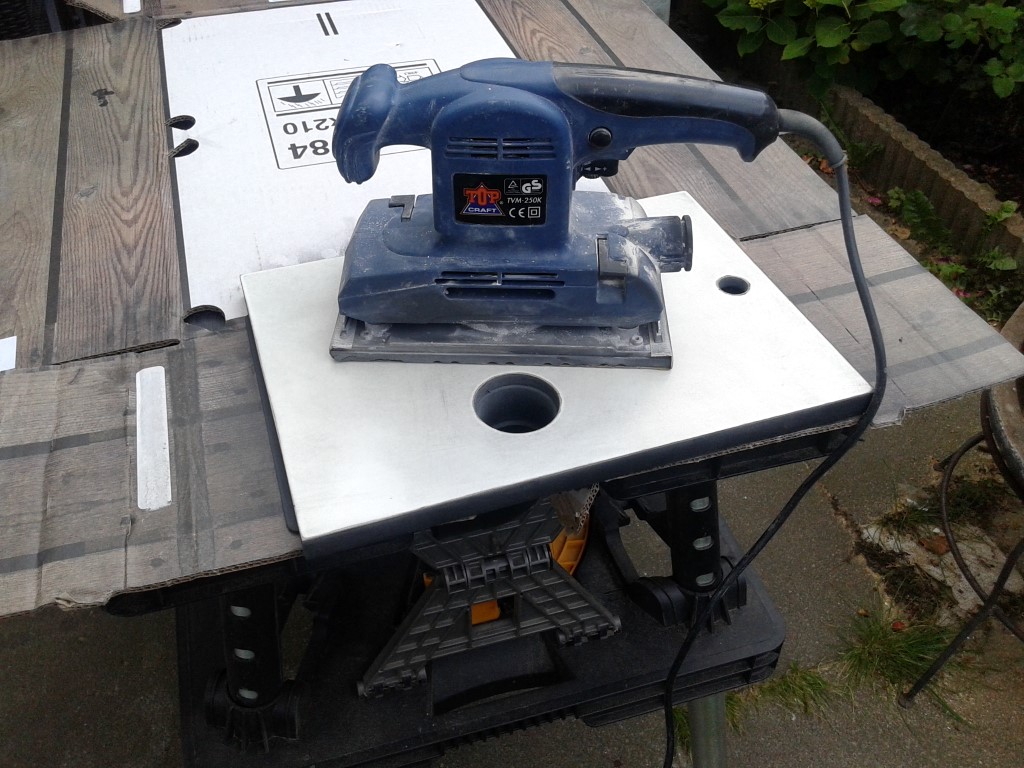
New primer on, drying time..
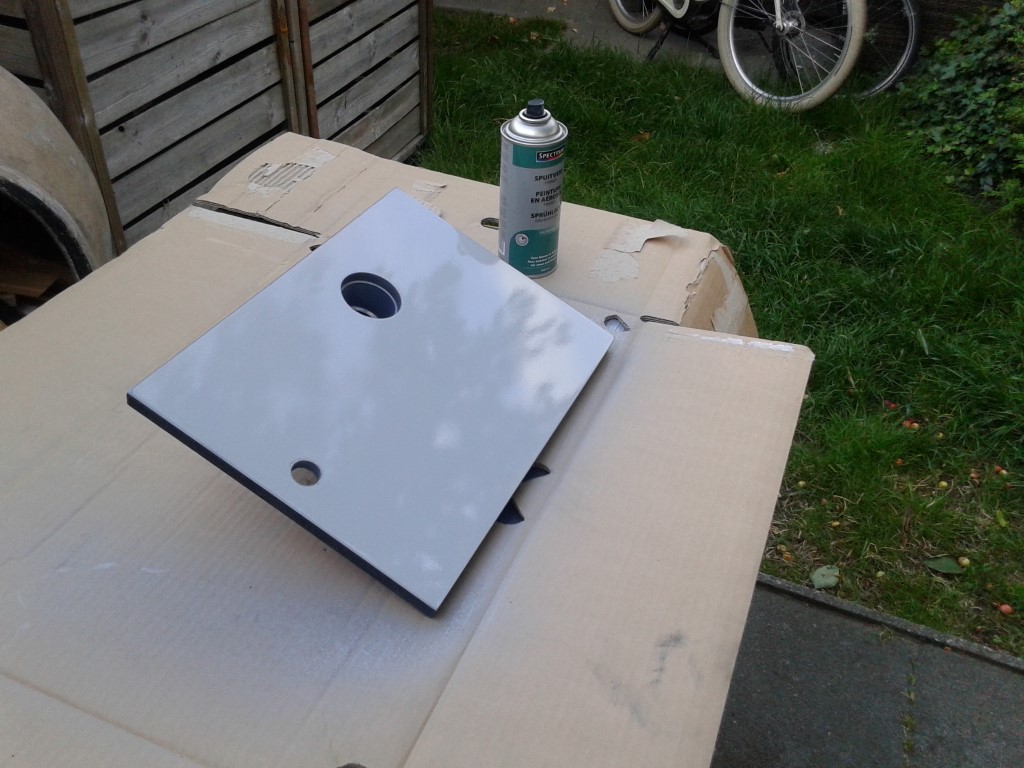
Here the same procedure as the backdoor lock, but this time on the control panel for the nut of the startbutton..
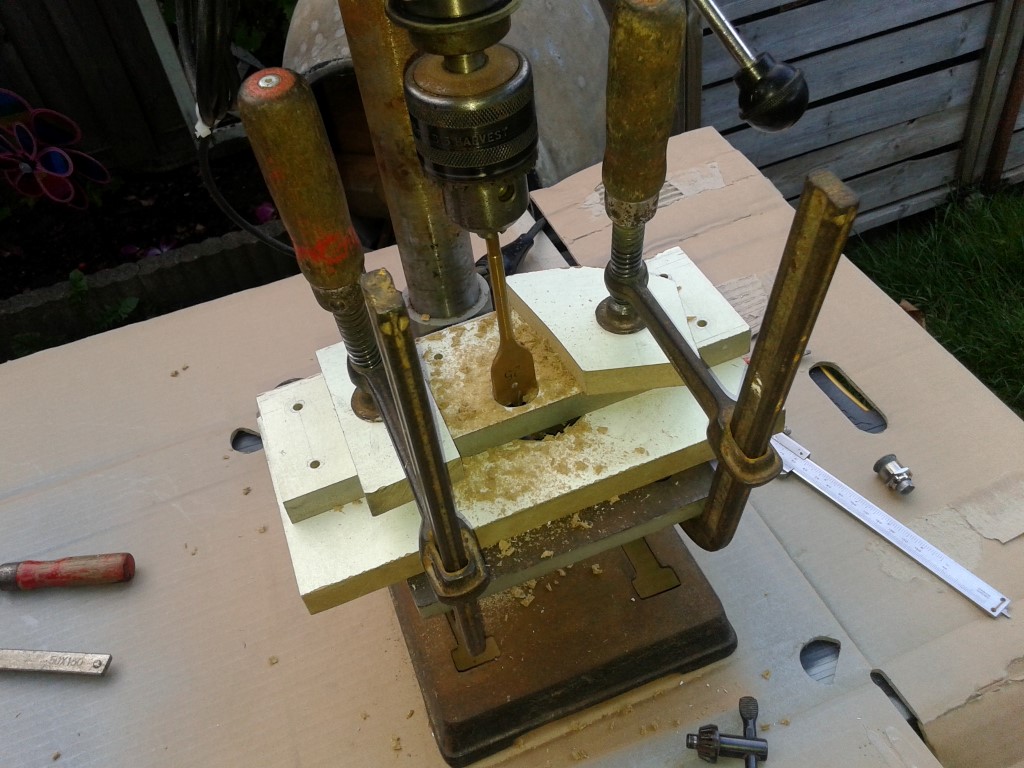
Again, Perfect fit !

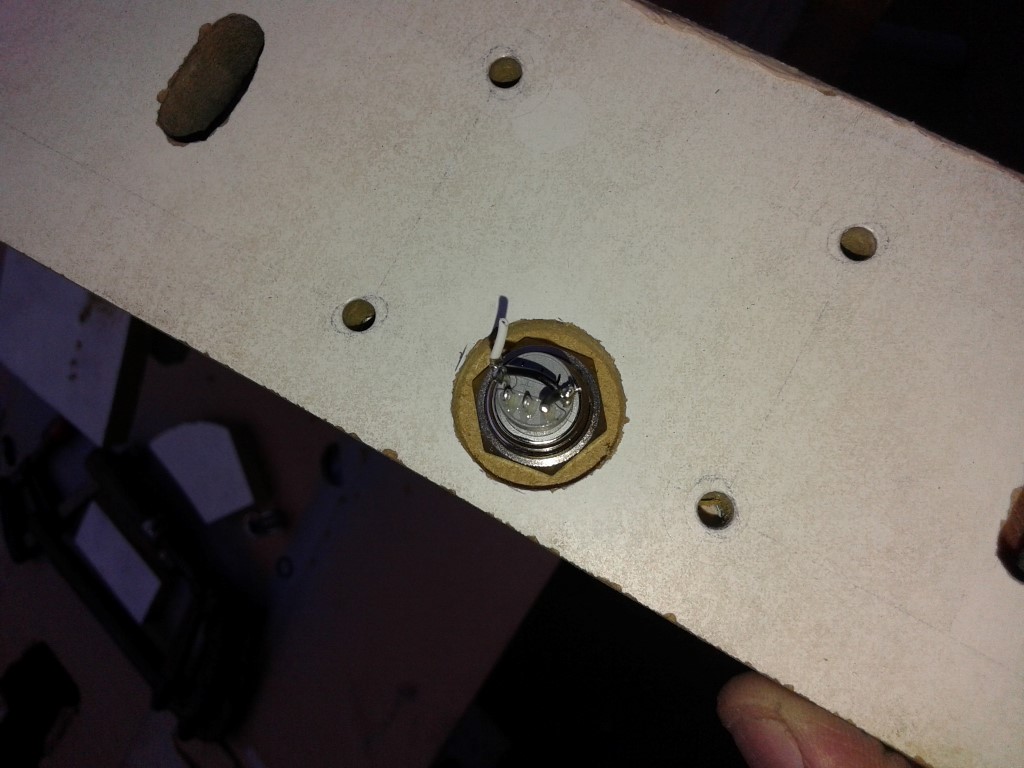
Another application of bondo, ready for sanding..
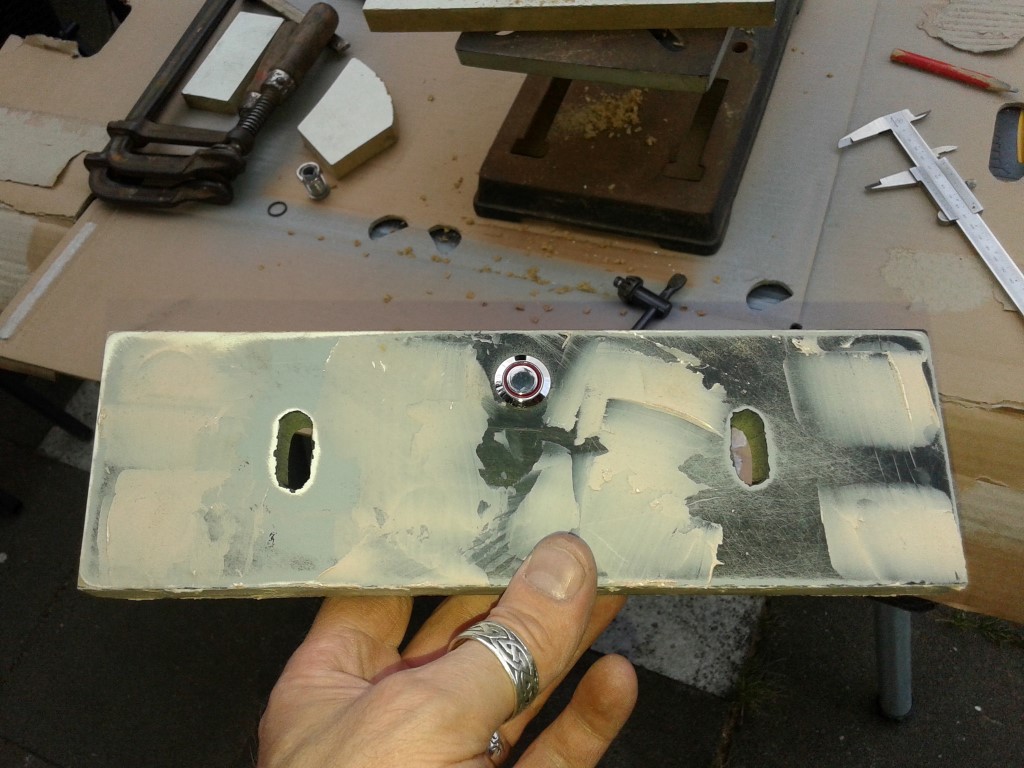
In the meantime the primer has dried enough to paint over with black..
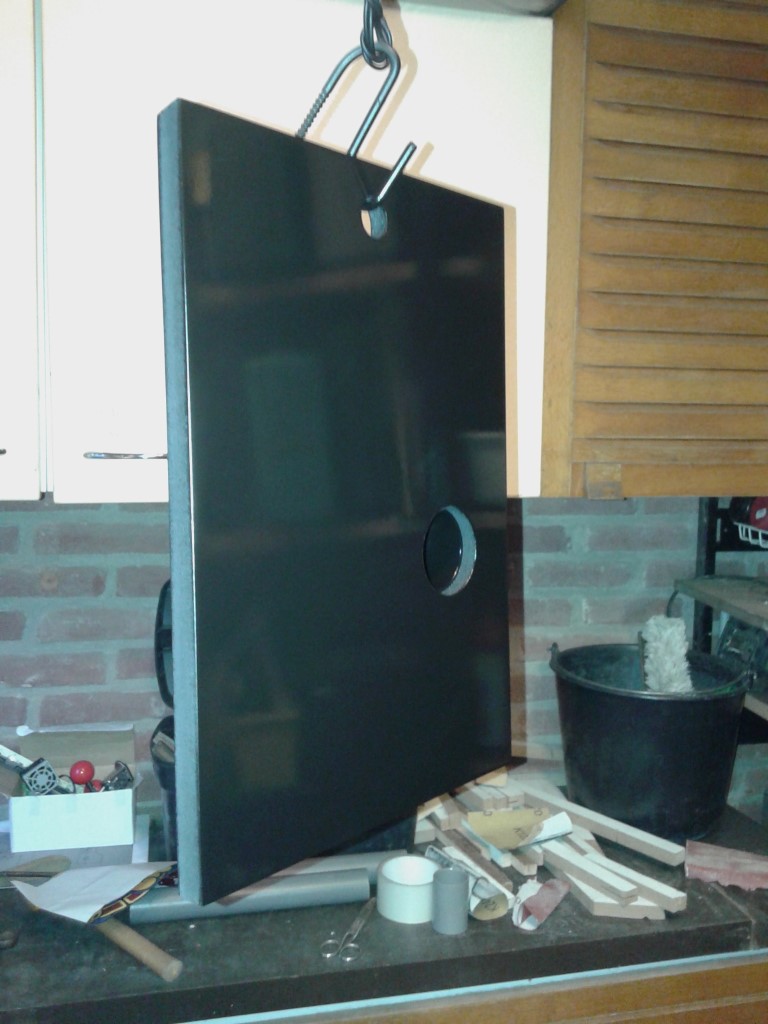
And after that i installed the salvaged fangrill..
A little bigger than the hole, but it will do ;)
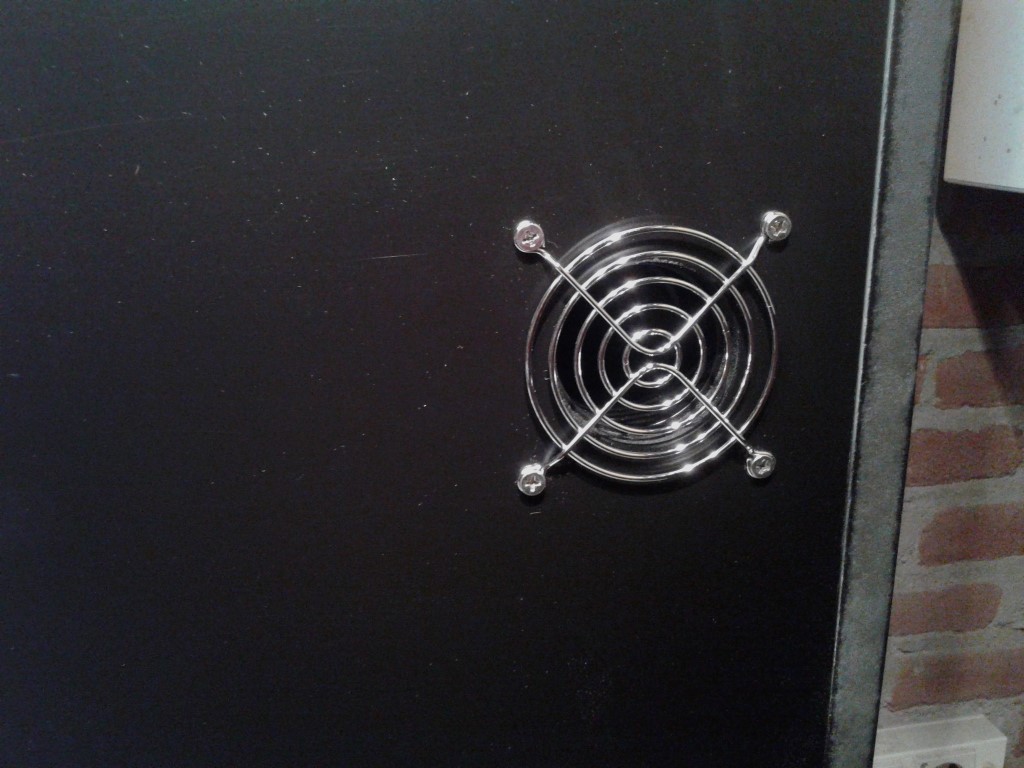
After a while it was still a bit too noisy for me, so i decided to also make an air inlet.
The outlet was really reducing the noise, but i figured i am already spending so many time to get this thing done right, i might as well take the extra step..
Let's see how many millimeters the pc is from the bottom of the cabinet..
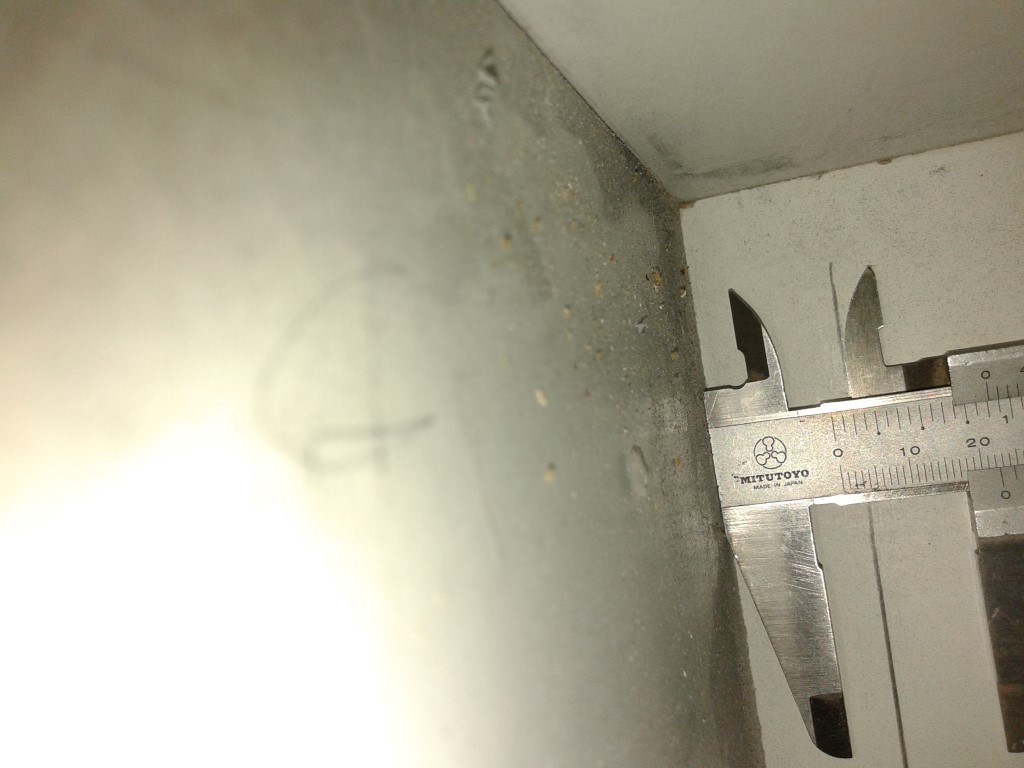
Drill a hole exactely where the inlet fan of the pc is located..
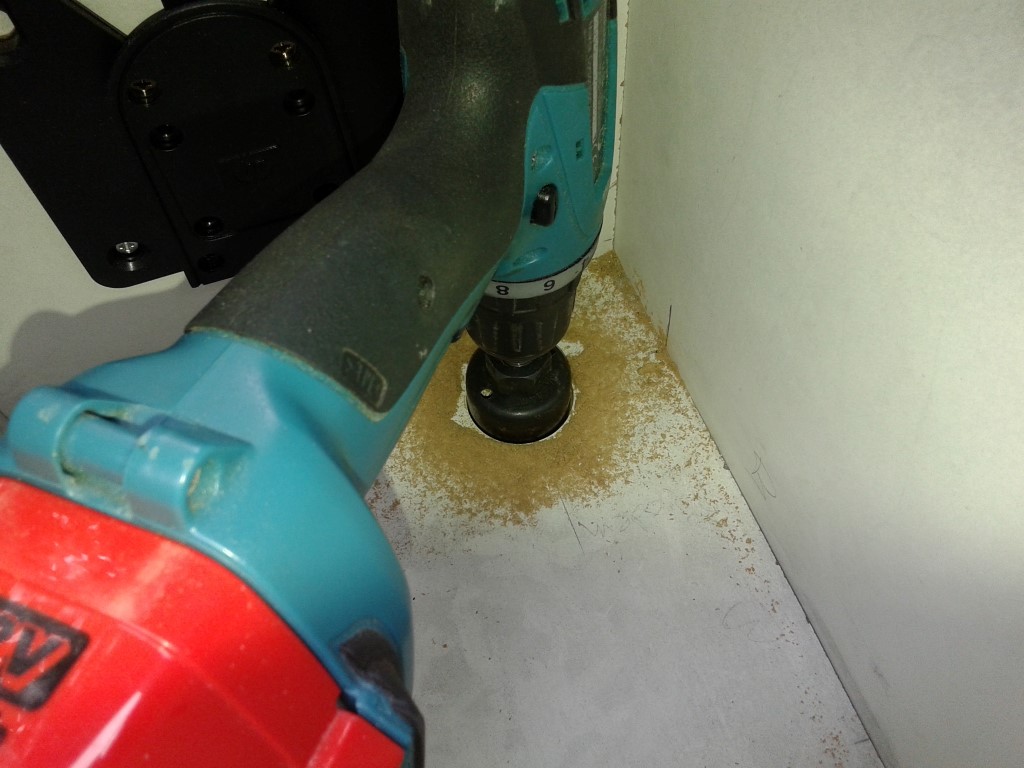
Insert a piece of PCV pipe in there to match the height..
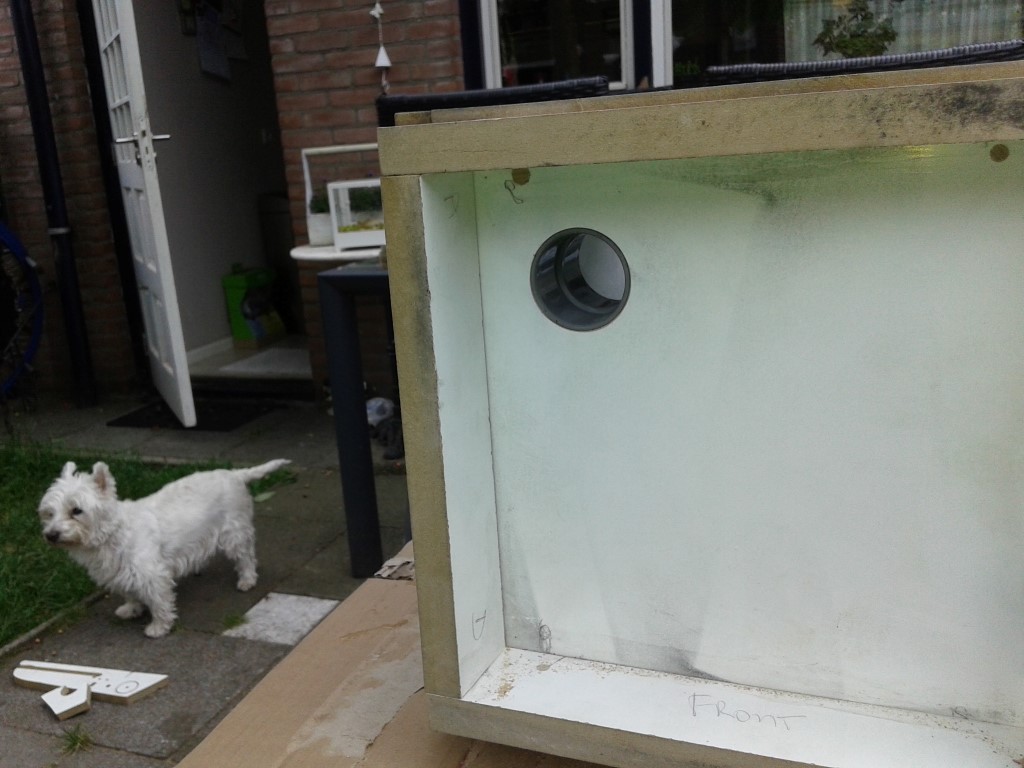
install a 90 degree piece to the back, and drill the other side in the base of the cabinet..
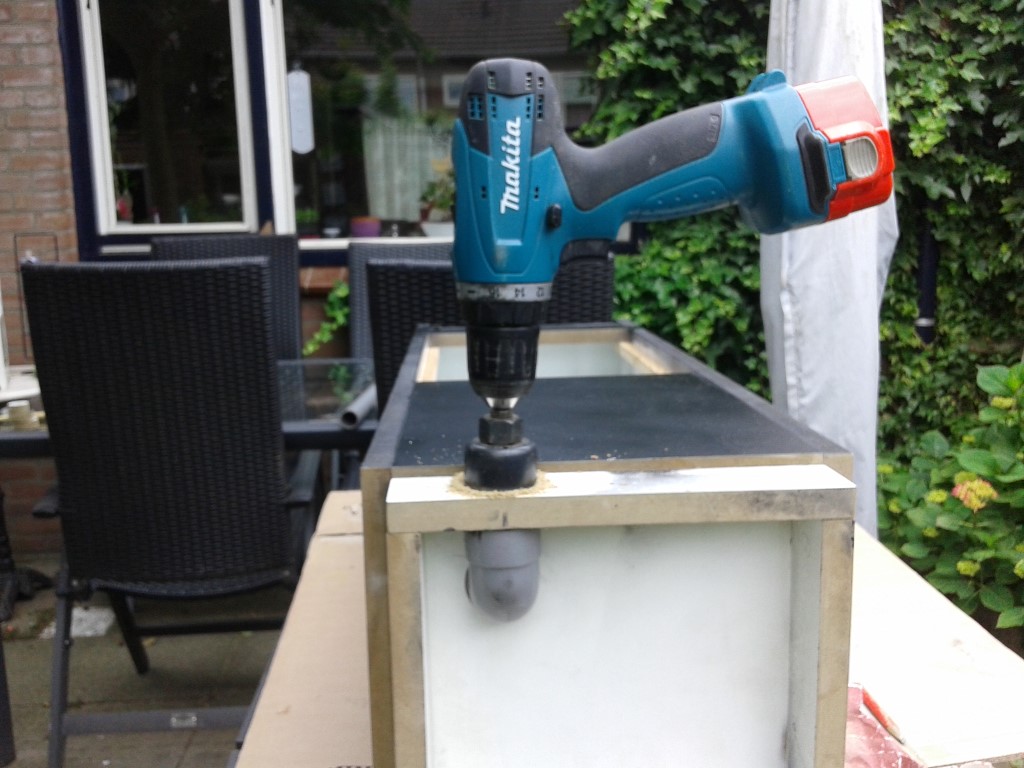
I tried to drill as high as i could..
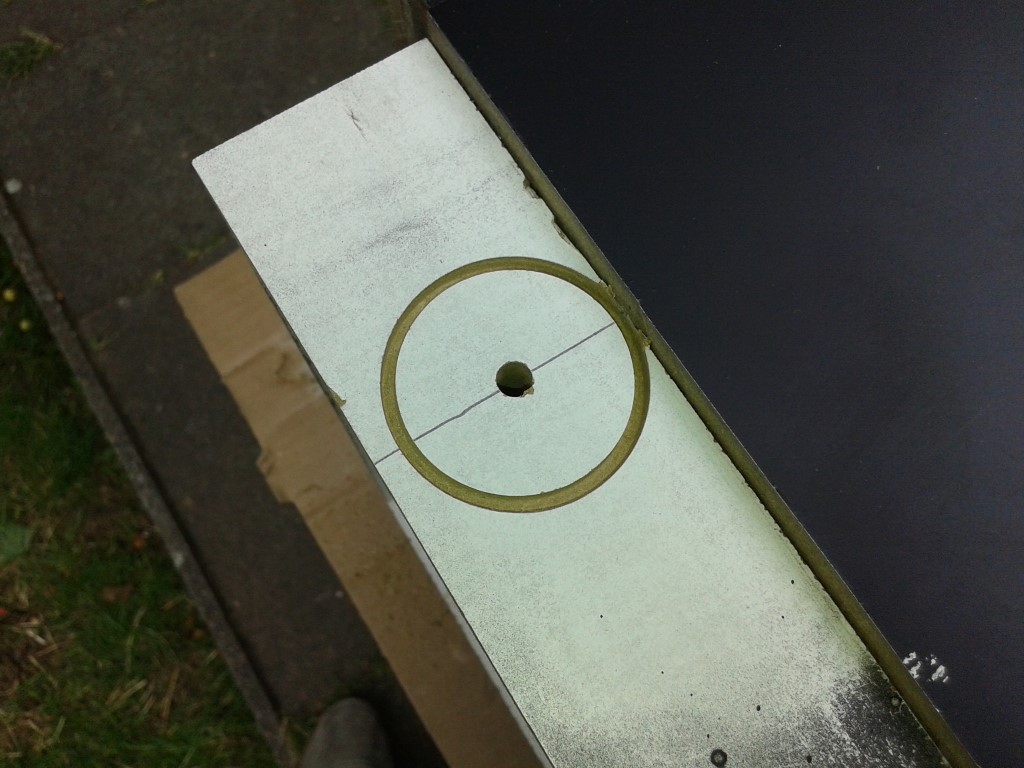
Perfect !

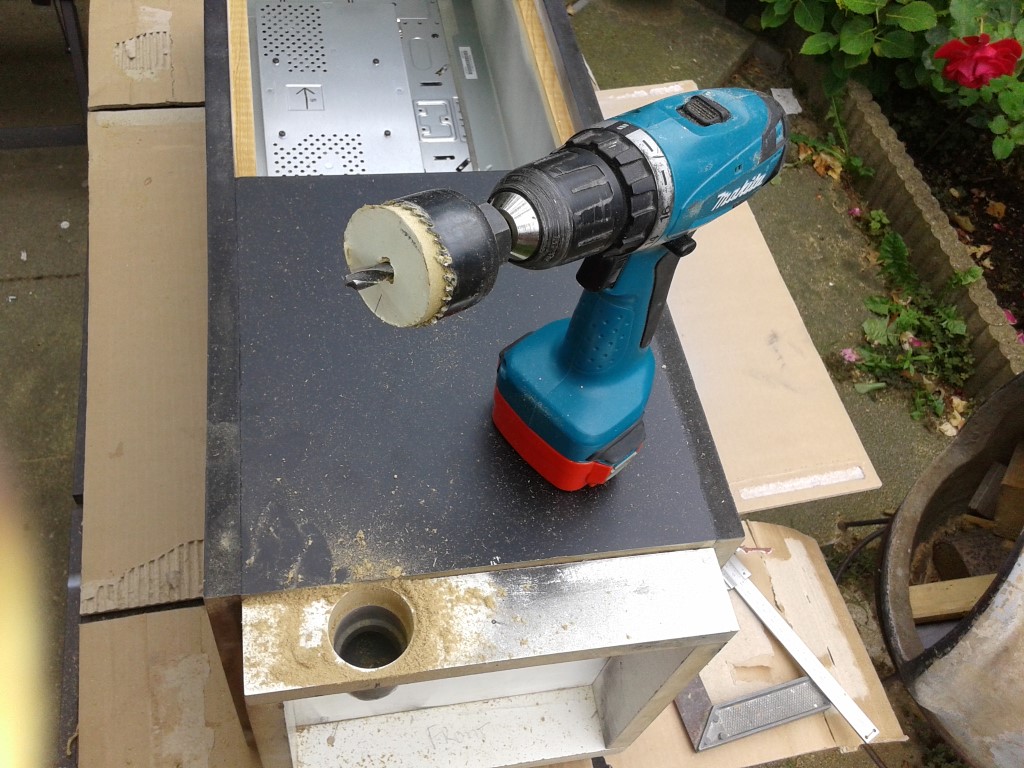
Fit another piece of PVC pipe in there and we have a nice inlet..
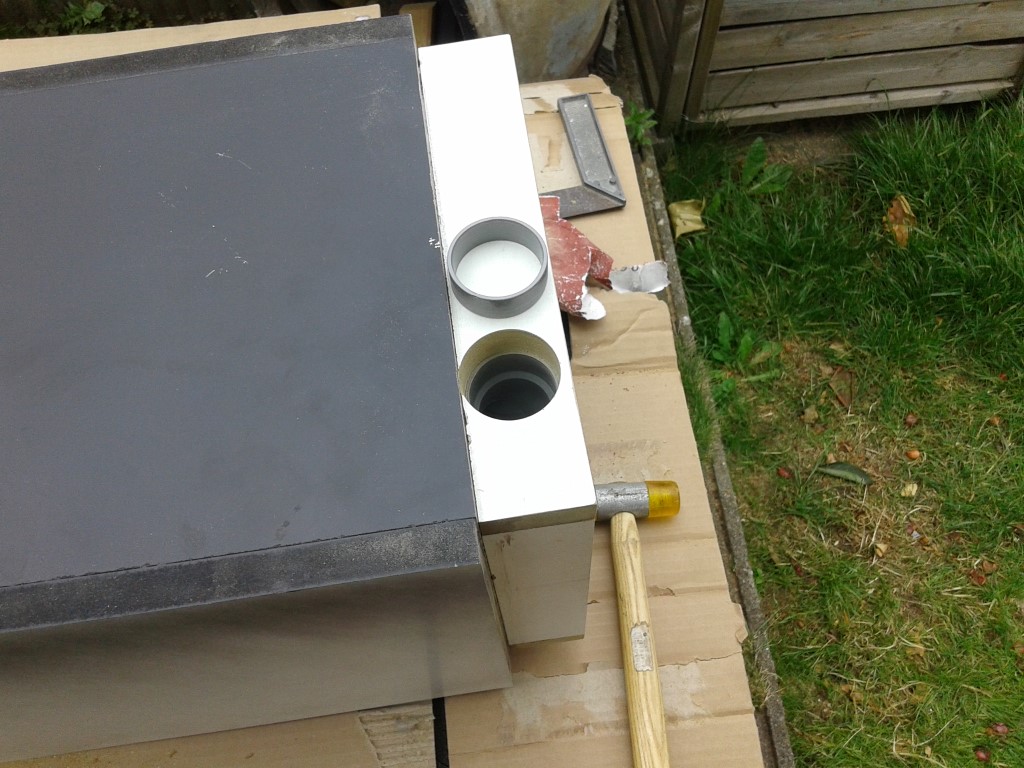
Spraypainted the bottom afterwards..
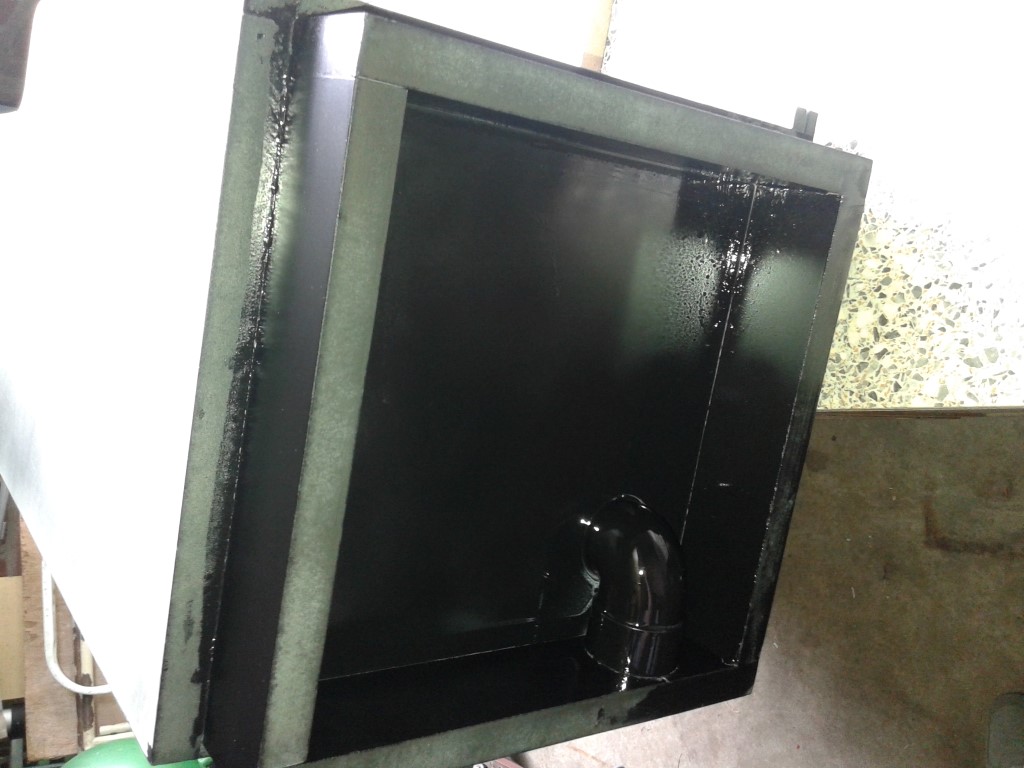
and spraypainted also the outside including the rest of the base which needed some paint also.
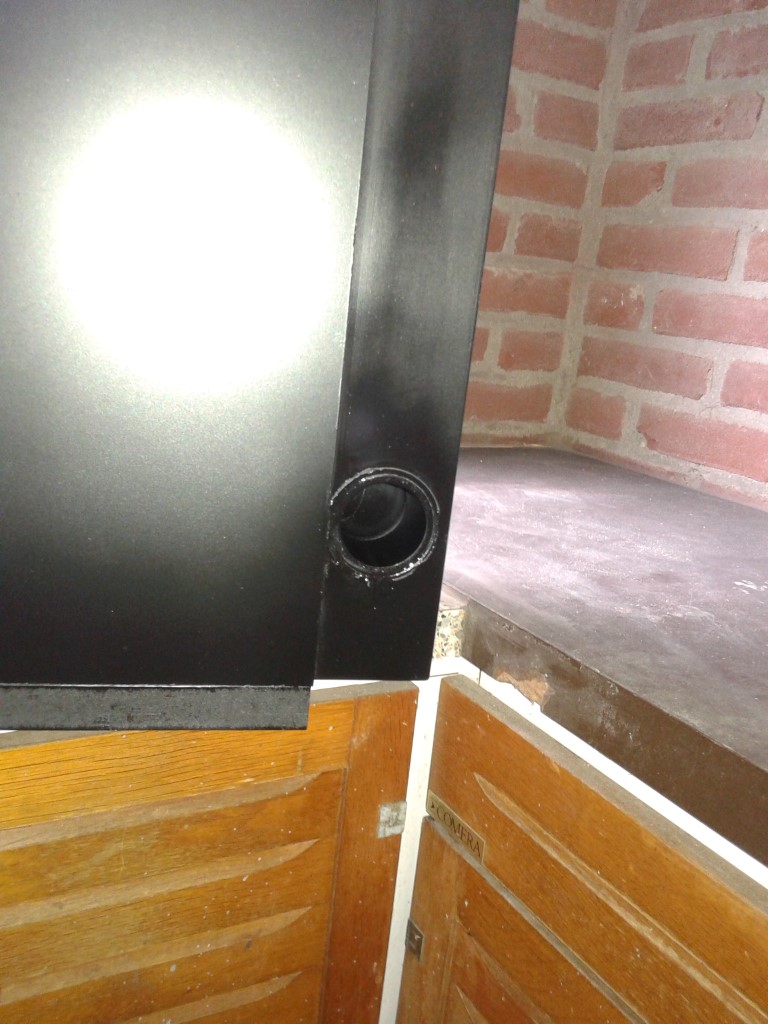
I was looking for another nice fangrill, but this location required a smaller one than the backdoor, and i could not find one at the time.
Perhaps in the future i will stumble over a suitable grill, but for now this will do ;)
After installing both ducts, silent as it can be.
Mission accomplished !